Potential for Circular
Economy in Infrastructure
and Industrial Power Plants
The
concept
of Circular Economy aims for restorative, regenerative, recycled,
reusable and inventive design. It reduces the dependency on natural
resources by encouraging the use of secondary resources such as
plastics, industrial waste, construction and demolition (C&D) waste for
production, thereby promoting efficient use of resources, addressing the
global resource scarcity and climate change. Moreover, massive
quantities of critical resources are extracted for production of
building materials.
The traditional clay brick sector in India
accounts for 5.5% of total greenhouse gas (GHG) emissions and depletes
approximately 500 million tonnes of cultivable topsoil. In the
end-of-life stage of buildings, 716 million tonnes of C&D waste is being
generated across the country annually. Hence, there is an urgent need to
foster a rethinking systems approach for integrating circular economy
principles across various sectors for green, equitable and inclusive
growth.
To address the same, the district
administration of Angul in Odisha came up with an ambitious
‘Vision-2023’ plan in February 2021. The objective is to create a
sustainable model making Angul self-reliant in its economy and natural
ecosystem. Angul is a highly industrialised district that provides 15%
of India’s coal and 5% of the country’s steel in addition to 5,000 MW
power supply, which is the overall generation from the district.
Besides, Angul is highly forested with 42% land in the district under
forest cover and 30% being used for agriculture. This makes it a
resource-rich district with high potential to explore the angle of
circular economy across these sectors.
During one of the field visits to Angul, the
Development Alternatives team observed that on-going construction and
demolition works in local infrastructure development projects such as
jails, schools and health centres generated a huge amount of C&D waste,
such as concrete, iron rods, wood and masonry waste, which holds
tremendous potential to be recycled and reused in ongoing construction
projects. During the visit to industrial power plants located at Kaniha
and Talcher, it was observed that about 3,000-20,000 metric tonne of fly
ash is generated every day which is being utilised for making various
products such as lightweight aggregate (LWA) which is highly durable and
greater in strength than the normal aggregate. They are also producing
paver blocks for internal infrastructure development and nearby villages
that fall under their CSR projects.
Fly ash is the by-product of thermal power
plants that results from the combustion of pulverised coal and is
transported from the combustion chamber by exhaust gases. Fly ash
utilisation has significant environmental benefits such as reduction in
GHG emissions, effective substitution of red bricks and in the
construction of highways. The Odisha MSME Development Policy of 2016
mandates the usage of fly ash bricks (FAB). The team observed that for
the construction of new jails and schools in Angul, FAB was being used
instead of red bricks.
As per the MOEFCC 2020 guidelines, National
Aluminium Company Limited (NALCO) is providing incentives, supplying fly
ash to SMEs brick-producing units and to National Highway Authority (NHA)
for making roads and highways. National Thermal Power Corporation’s (NTPC)
research wing is also carrying out final testing on conversion of fly
ash to sand in collaboration with NTPC Energy Technology Research
Alliance (NETRA), New Delhi.
It was observed that in the industrial power
plants, the process of aluminium- and steel-making generated waste such
as slag, sludge and metal craps. Industrial waste is defined as waste
generated by industrial processes which has a huge scope to be reused
and recycled resulting in a cleaner production of services. For example,
granulated sludge can potentially be used to prepare sand with higher
resistive qualities than natural sand which may reduce harmful sand
mining practices. Industries are also supplying blast furnace slag to
cement producing companies in Karnataka as an effective additive in the
cement manufacturing process.
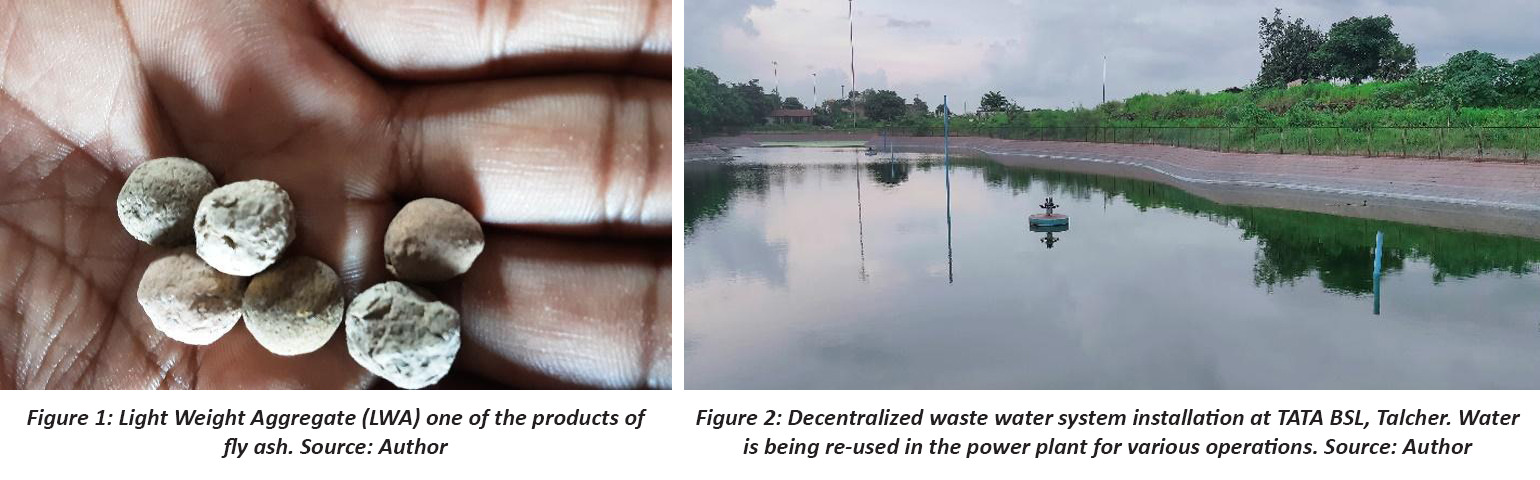
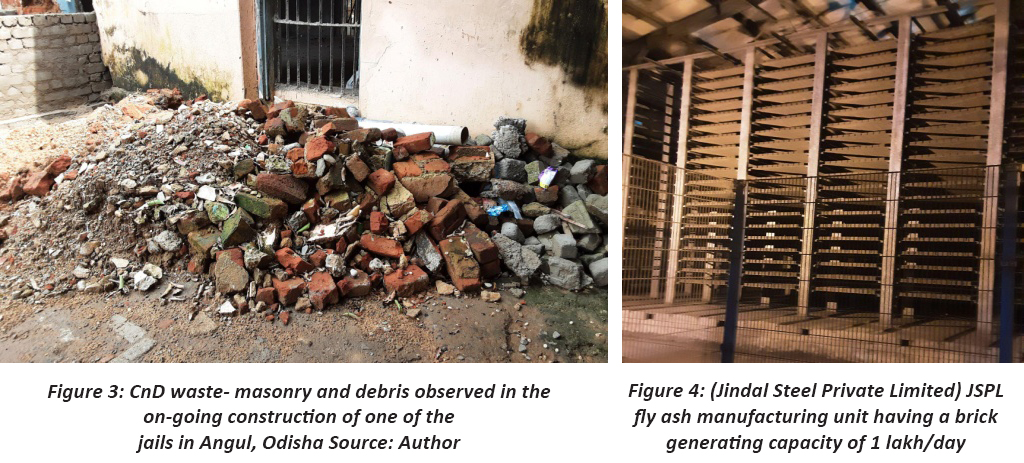
Angul district currently has low scores on
human development parameters and is prone to climate change due to
imbalance in the consumption of natural resources. The bright side is
that being a resource-rich, industrial district, it generates
appropriate revenues to take decisive action. Hence, it is important
that stakeholders such as government authorities, NGOs and line
departments come together on a common platform through the creation of
institutional mechanisms such as agile sustainable procurement policies
using tools such as circular economy dashboards and adopting frameworks
for improved data-based decision-making such as PEST (Political,
Economic, Social and Technological) analysis and LCA (life cycle
assessment) to evaluate the environmental burdens associated with
materials used and wastes released to the environment for robust
data-based decision making.■
References:
Rashi Sirohi
rashi@devalt.org
Back to Contents
|