Waste to
Wealth Creation
using Kota Stone Waste
India
contributes to 17.7% of the world’s population; which is expected to
grow to 1500 million by 2030 and 1600 million by 2047, making it the
most populated nation in the world (BMTPC, 2018). Population,
urbanisation and income growth is expected to increase over the next few
decades which will increase material consumption. Simultaneously, waste
generation will also increase multiple fold. A detailed study on the
solid waste generation in India conducted by Pappu et al. (2007)
estimated that 960 million tonnes of solid waste (hazardous or
non-hazardous) is generated in India annually during different processes
which include industrial, mining, agricultural and municipal activities.
Several efforts are being made across the country to utilise different
streams of waste and use them as alternative materials in different
sectors to reduce the burden on virgin natural resources and safeguard
the environment from unethical disposal of waste.
In this article, we will focus on one such
waste stream, the Kota stone waste which is generated as a byproduct of
the mining sector. Kota stone is primarily a calcareous rock of
sedimentary origin which generally consists of 68 to 70% calcium
carbonate and 23 to 25% silica. Kota and Jhalawar districts of Rajasthan
and Neemuch district of Madhya Pradesh are the major producers of Kota
stone dust. It was estimated that Kota stone production amounted to 80
lakhs million tonnes per annum. Out of this about 4 to 5 lakh million
tonnes is fine dust generated from quarrying, crushing and polishing
which is dumped in surrounding agricultural fields, road sides and
forest lands (Hussain and Perez, 2015).

As Kota stone dust is a good source of
carbonate, it can be used as a replacement for limestone in ternary
blends (Krishnan et al., 2018; Weerdt et al., 2011). Ternary cements
have been gaining importance due to their improved performance and
synergistic benefits on using in combination with supplementary
cementing materials (SCM). In ternary cements, low clinker factor can be
achieved by replacing clinker with industrial wastes (Jittin et al.,
2020). Limestone calcined clay cement or LC3 is one such ternary cement,
in which clinker factor of 0.50 has been achieved by partially replacing
clinker using a combination of calcined clay and limestone (Avet et al.,
2018; Emmanuel et al., 2016).
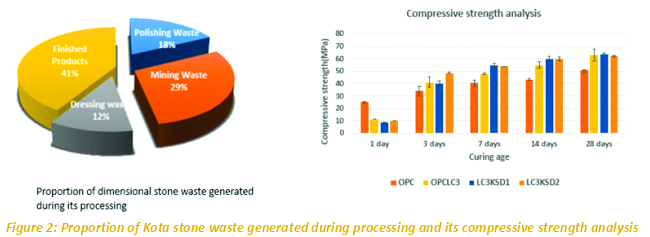
To meet the economic goals without affecting
the climate mitigation goals of the nation, shift to alternative
technologies and use of waste along with conventional technologies
becomes crucial. As cement production leads to degradation of the
environment in many ways, use of Supplementary Cementitious Materials (SCMs)
as a substitution of clinker could be a solution for the demand of
cement to be met. The use of SCMs must be assessed locally based on
their availability and properties. Thus, in the current research study,
Kota stone dust has been used as a replacement of limestone in producing
LC3 cement. Two different blends were prepared with 16% Kota stone dust
(LC3KSD1) and 23% Kota stone dust (LC3KSD2). Refer to Figure 2.
With the increase in the amount of Kota
stone dust from 16% to 23%, the early strength increases and the later
age strength is approximately similar, hence we can increase the amount
of Kota stone dust without compromising on its compressive strength. The
analysis is that we can utilise waste Kota stone dust in place of
limestone as there was no effect observed on the compressive strength at
various ages.
■
References:
1. Avet, F., & Scrivener, K. (2018). Investigation of the calcined
kaolinite content on the hydration of Limestone Calcined Clay Cement
(LC3). Cement and Concrete Research, 107, 124-135.
2. Emmanuel, A. C., Haldar,
P., Maity, S., & Bishnoi, S. (2016). Second pilot production of
limestone calcined clay cement in India: the experience. Indian Concr.
J, 90, 57-64.
3. Hussain, A., & Perez, I.
(2015). V.,“Kota stone slurry problem and possible solution”.
4. Jittin, V., Rithuparna, R.,
Bahurudeen, A., & Pachiappan, B. (2020). Synergistic Use of Typical
Agricultural and Industrial By-products for Ternary Cement: A Pathway
for Locally Available Resource Utilisation. Journal of Cleaner
Production, 123448.
5. Krishnan, S., Emmanuel, A.
C., Kanaujia, S. K., & Bishnoi, S. (2018). Hydration and mechanical
properties of limestone calcined clay cement produced with marble dust.
In Calcined Clays for Sustainable Concrete (pp. 249-253). Springer,
Dordrecht.
6. Pappu, A., Saxena, M., &
Asolekar, S. R. (2007). Solid wastes generation in India and their
recycling potential in building materials. Building and environment,
42(6), 2311-2320.
7. Utilisation of Recycled
Produce of Construction and Demolition Waste: A Ready Reckoner (BMTPC,
2018)
8. Weerdt, K., Haha, M. B., Le
Saout, G., Kjellsen, K. O., Justnes, H., & Lothenbach, B. (2011).
Hydration mechanisms of ternary Portland cements containing limestone
powder and fly ash. Cement and Concrete Research, 41(3), 279-291.
Aayushi Agrawal, Neha Agarwal
aagrawal@devalt.org, nagarwal@devalt.org
Back to Contents
|