Limestone Calcined Clay
Cement:
From Research to Practice
It
is now well understood that the most viable alternative to reduce the CO2
impact of cement (and therefore, concrete) is the use of supplementary
cementing materials (SCMs). The reduction in clinker factor of cement
can also prolong the life of limestone reserves, making it possible to
continue using cement as a major binding material for concrete.
Among the available SCMs,
the only ones that are potentially available in significant quantities
are fly ash, calcined clay and limestone. The large-scale use of fly ash
is hampered because of the high degree of variability in the properties
of fly ash, making the overall availability of suitable fly ash limited.
While calcined clay or limestone can only be used at relatively low
replacement levels (10 to 25%), the combination of calcined clay and
limestone has presented a possibility of large replacement of cement
clinker. The blend of limestone and calcined clay in a ternary
combination with cement results in a significantly improved performance
of mortars and concretes because of:
(i) Formation of new
hydrated phases leading to an improved micro-structure with low porosity
at early ages and
(ii) Improved particle
packing leading to a dense system.
A recent collaborative
project between Ecole Polytechnique Federale de Lausanne (EPFL) in
Switzerland and IITs - Delhi, Madras and Bombay along with TARA, the
social enterprise wing of the Development Alternatives Group in India,
has looked extensively at the production and performance of such blended
cementitious systems called Limestone Calcined Clay Cement or LC3.
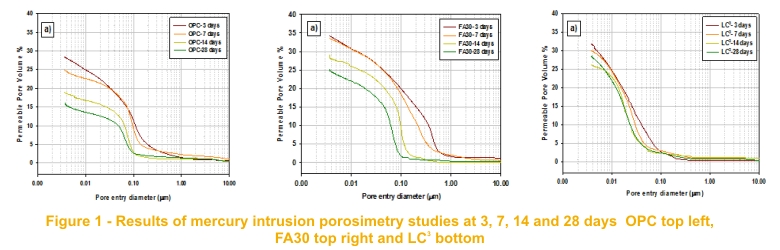
The development of the
denser pore structure in LC3 systems is depicted in the
results of mercury intrusion studies in Figure 1. Pores are classified
as capillary pores (inter-particle spaces, large 10 µm - 50 nm and
medium 50-10 nm), gel pores (fine pores between hydrates, 10 nm 2.5 nm)
and interlayer pores (within the hydrates, < 0.5 nm). Based on this
assessment, it is clear that the LC3 system has more of the
finer pores, indicating a greater amount of the hydrated gel, as
compared to the fly ash system. This shift to finer pores happens as
early as 3 days. While there is almost no difference between LC3
and OPC systems at 7 days, the fly ash system is able to achieve
equivalent dense structure only after prolonged curing. Studies on
compressive strength development with the three binder systems also
showed that a lower cementitious materials content and higher w/c in LC3
concretes was able to produce equivalent strength in concrete.

The benefits of the
denser pore structure were also seen in the durability results. The
charge passed in 6 hours in the Rapid Chloride Permeability Test (RCPT)
as per ASTM C1202, for ordinary strength grade (M30 M50) concretes with
LC3, was in the 'Negligible' range (see Figure 2), indicating
a performance level comparable with ultra high strength concretes that
have very low w/c (< 0.20). In comparison, the fly ash concrete was only
able to reduce the permeability to the 'Very Low' level, that too only
by 90 days. The rapid chloride permeability test is only one major
indicator of the level of durability. Several other durability tests
conducted at IIT Madras, including the Rapid Migration Test, Oxygen
Permeability Test, Water Sorptivity Test, and Bulk Diffusion Test - all
pointed to a superior durability attained with the LC3
binder. In short, the performance of concrete with LC3, in an
environment which promotes chloride induced corrosion, is superior to
that of concrete made with plain OPC, or even with a fly ash based
concrete. The one possible negative could be the performance of LC3
binder in carbonation prone environments. This occurs
in polluted areas, under specific conditions of humidity (usually RH
between 50 and 70%). Carbonation leads to a gradual reduction in
alkalinity of the concrete, and creates the depassivation of reinforcing
steel leading to its corrosion. Howeve r, the lower permeability of the
concrete with LC3, combined with the high resistivity of the
system, would even cause a lowering of the corrosion potential in such
environments. Extended studies to assess the corrosion of reinforcing
steel in carbonation prone conditions are currently under way.
While there are several
positives in terms of durability performance, the real benefit of using
the LC3 binder is realised in the CO2 footprint of
the concrete. Figure 3 shows the CO2 emissions per kg of
concrete produced for concretes with OPC, 30% fly ash, LC3
and 15% slag. It is clear from the data that the major contribution to
the emission is from the cement component in concrete and the lowering
of emissions with LC3 in an equivalent grade of concrete is
significant as compared to OPC and better than for fly ash and slag
based concretes.
In conclusion, there is
tremendous potential for the use of LC3 in concrete, but
there are several more steps before this technology can be properly
implemented. These include the standardisation of cement, addressing the
issues related with selection of materials and production and showcasing
the technology in demonstration structures. Further, the true
environmental impact over the service life of a concrete structure in
practice needs to be ascertained. Efforts to standardise the cement in
India are ongoing. The cement companies have a crucial role to play in
up scaling of this technology. The current phase of the collaborative
project aims to address these issues. ■
Manu Santhanam
Professor, Civil Engineering
IIT Madras
manusanthanam@gmail.com
Endnotes
-
K.L.
Scrivener, Options for the future of cement, Indian Concrete Journal
(2014) 1121.
-
S.
Bishnoi,S. Maity, A. Mallik,S. Joseph, andS. Krishnan, Pilot scale
manufacture of limestone calcined clay cement: The Indian experience,
Indian Concrete Journal (2014) 2228.
Back to Contents
|