A Cluster Approach To
Sustaining
Fly Ash Brick Enterprises In Bihar
Bihar
is one of the fastest growing states in India. Propelled by its economic
and population growth, it is witnessing a boom in its construction
sector, and there is increasing demand of bricks as a major building
material. Bihar has about 7,700 clay brick kilns1 with an
annual production of approximately 23 billion bricks2, and
holds the largest production share of about 97% in the state’s brick
industry. The clay brick industry currently is based on a decentralised
production activity using energy intensive, resource depleting and
highly polluting technologies and production methods. The sector
provides seasonal employment to large number of labourers, but the
production process involves use of fertile soil, which is in direct
conflict with the agricultural sector. Curbing this challenge is
essentially crucial for Bihar being an agricultural economy. For the
state of Bihar to ensure that the state’s economic growth is not at the
cost of environmental and public health, it is extremely important to
take initiatives to promote cleaner brick technologies and waste
management. In the given situation, encouraging the production and usage
of fly ash bricks in Bihar is an opportunity for transition towards
resource efficient bricks while providing decent jobs to the local
community.
Fly ash bricks are very resource efficient,
least energy intensive and much greener alternates to other types of
bricks. In comparison to burnt clay bricks, each fly ash brick conserves
3kg of top soil, 0.024kg of coal, and mitigates 0.077kg of CO2
emissions. The social, economic and environmental benefits of fly ash
bricks are immense. However, the fly ash brick industry in Bihar has
been struggling to gain a fair share of market in the state’s brick
industry. The industry is plagued by various challenges that have become
barriers to its upscaling. These challenges are majorly
related to timely availability and quality of raw material, awareness
about fly ash brick among the general public, ease of access to finance
and technology know-how, enforcement of government policies and
competitiveness. Moreover, most of these enterprises work and suffer in
individuality, lacking vision and collective action plan to uplift the
industry. Given the importance and urgent need of resource efficient
green building materials like fly ash brick, a cluster-based approach
for sustainability of fly ash brick enterprises is a must.
The Development Alternatives (DA) Group has
been implementing measures under its cluster development approach to
promote and sustain Fly Ash Brick (FAB) enterprises in Bihar. DA’s
methodology broadly includes identification of potential FAB clusters,
selection, diagnostic study, action plan, implementation and monitoring
and evaluation (M&E). Stakeholder management for trust building and M&E
form an integral part of the cluster development process from ideation
to successful implementation.
Demand versus availability of FAB has been a
topic of constant debate in various state level meetings conducted in
Bihar. Quality of FAB has also been flagged as a major concern. To
address these concerns, DA Group, in 2018, carried out a survey of all
38 districts in Bihar and mapped the FAB enterprises on an interactive
Geographic Information System (GIS).
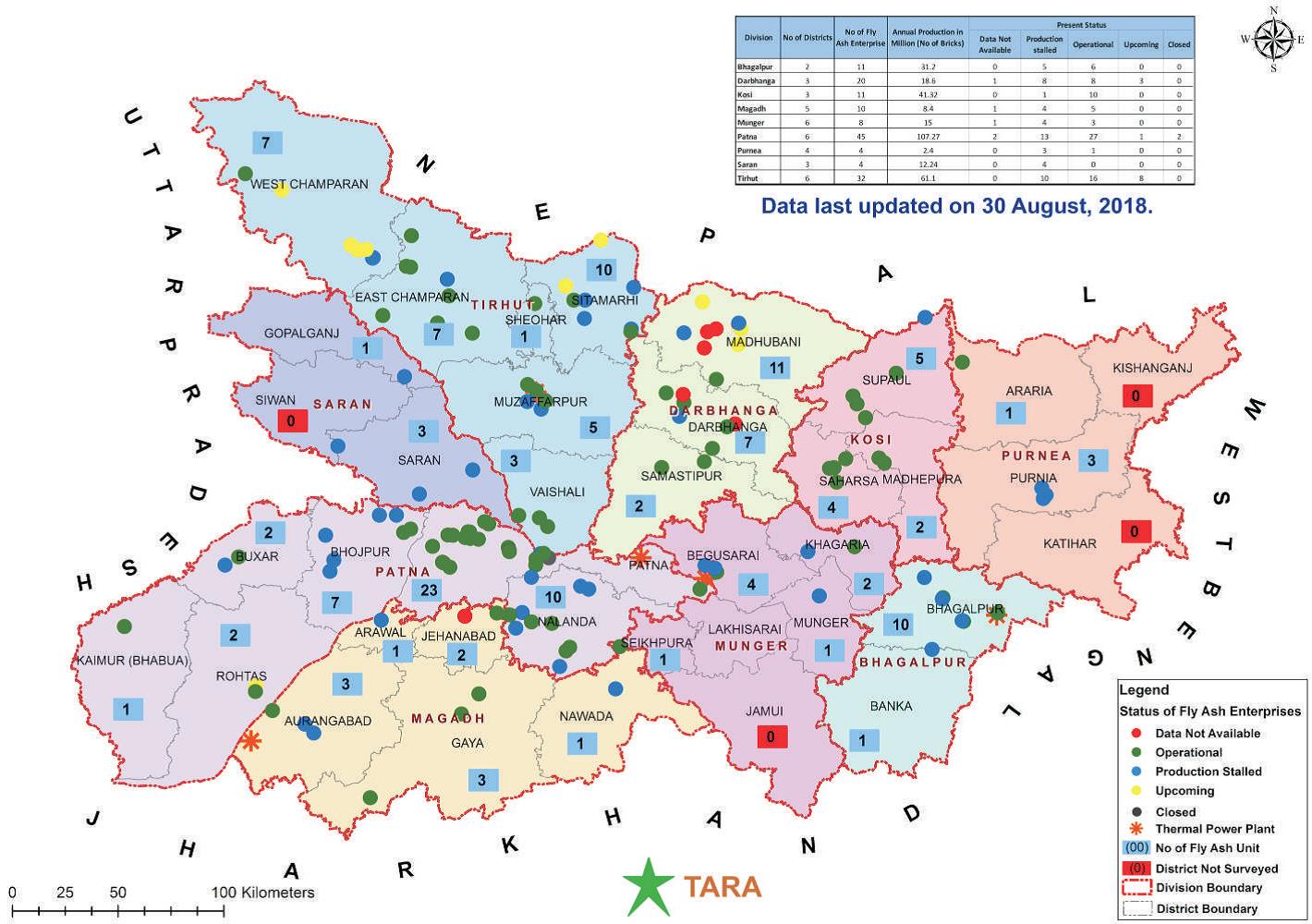
The ellipses on the map (shown above)
identify potential clusters that could be developed with support from
government and private stakeholders.
Key highlights
-
For the first time in Bihar, fly ash brick
(FAB) enterprises were surveyed and mapped on an interactive GIS.
-
The survey recorded 145 FAB enterprises with
installed production capacity of 0.3 billion FAB per year, of which 36
have enrolled under FAB Quality Improvement Programme by TARA – the
social enterprise wing of the Development Alternatives Group, and 31
have been imparted onsite technical training on it.
-
Notification mandating use of 100% FAB in
departmental projects has been reinstated by Building Construction
Department, Government of Bihar.
-
Wealth of new data on status of FAB
enterprises is available in the public domain to inform future policies
and the effectiveness of existing policies.
TARA is also leveraging public and private
support institutions to facilitate creation of Common Facility Centre
(CFC) and infrastructure development for the FAB clusters. A CFC
includes facilities like testing, training, design, marketing
display/selling, effluent treatment, logistics, raw material bank/sales
depot, etc. Similarly, infrastructure development consists of facilities
like power distribution network, water, telecommunication, drainage and
pollution control facilities, roads, banks, raw material storage and
marketing outlets, common service facilities and technological backup
services. These facilities support sustainability and growth of FAB
enterprises by addressing common issues such as improvement of
technology, skills and quality, access to quality raw material, market
and capital.
■
Sudhir Sah
ssah@devalt.org
References:
1 Source: Ministry of Mines, 2018
2 Average annual brick production of 1 Fixed Chimney Bull’s
Trench Kiln (FCBTK) is 30 lakh. Assuming all bricks kilns are
functional.
Back to Contents
|