Clean Building Technology
Transfer to Malawi
The
Republic of Malawi is a land locked country situated in Southern Africa.
With a population of around 17.6 million, average growth rate of 2.9%
and an average annual per capita income of USD 402.4 , it is among the
poorest countries in the world. According to the projection made by a
population census (NSO 2008, pp. 26), the total rate of urbanisation in
the country is projected to reach 50% by 2050. This immense pace of
urban growth will put tremendous pressure on the country’s fledgling
building material sector.
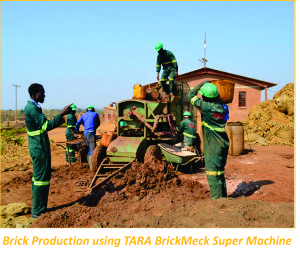
Currently, brick production in Malawi is
highly decentralised and unorganised. The entire Malawi brick industry
uses open clamps for firing. There is no control over the firing process
in the clamps. Lack of appropriate technology and know how in the
Malawian brick manufacturing sector results in irregular bricks in terms
of shape, size and quality. The sub-standard bricks can compromise the
integrity of the structures depending upon the construction practices
used. Primarily, the fuel used in firing bricks in Malawi is fuel wood.
It is estimated that around 850,000 tonnes of fuel wood will be required
annually to produce bricks for satisfying demands for housing, in the
absence of cleaner alternatives.
In an effort to address the challenges of
improving the brick industry in Malawi, CCODE undertook a study on
energy efficient and environmentally friendly methods of brick
production. The study identified the Vertical Shaft Brick Kiln (VSBK),
the most energy-efficient brick technology in the world, as a promising
solution . Thus, CCODE after having carried out a feasibility study in
2012 and a baseline study in 2013 ventured towards creation of the
enterprise Eco-Matters Ltd, which involved the construction of a VSBK
pilot plant, colloquially called the EcoKiln.
Meanwhile, CCODE with support from GIZ, TARA
(the social enterprise wing of the Development Alternatives Group) and
several other organisations has successfully piloted the VSBK technology
in Malawi. In parallel, dissemination workshops have been carried out
with the aim of creating more awareness among Malawian entrepreneurs.
The initiatives are meant to promote a larger agenda of introduction of
cleaner building material technologies in Malawi, going beyond the
EcoKiln. The technology transfer process was anchored for the past
couple of years through local Malawi institutions e.g. Eco-Matters Ltd.,
NCIC, TEVETA with support from Homeless International, UK and DFID
(India), in addition to GIZ.
Moreover, in order to build resilience of
communities against flooding caused by cyclone Idai and to help in
reducing the occurrences of flooding during such events, the project
titled ‘More Income and Employment in Rural Areas of Malawi’ (MIERA),
currently in phase III, proposes to expand the existing programme for
the dissemination of environmentally friendly building material
production technologies to the regions affected by Idai. Being good in
quality and conforming to Malawi Bureau of Standards norms, these bricks
made out of EcoKiln technology will improve the quality of houses and
provide much-needed alternate livelihoods to Idai affected people.
Case Study: Vertical Shaft Brick Kiln for
LC3 Production in Malawi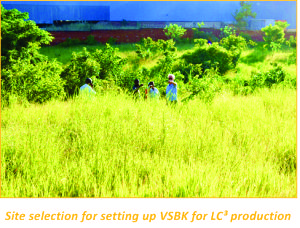
Lafarge Cement Malawi is a member of the
Lafarge Holcim group established in 1968. Lafarge is currently operating
a grinding unit in Blantyre and is the market leader in cement
production and innovation. It produces four cement products namely:
DuraCrete (CEMII 32.5N), Kumanga (MC 22.5X), Supaset (CEMII 42.5R) and
Khoma (MC5).
In the recent past, most of the clinker used
by Lafarge was imported from other countries to Malawi. However due to
rising transportation costs both by sea and land, import of clinker and
grinding in Malawi is becoming less economically feasible. Moreover, due
to relaxation in import license of cement by the Malawian Government,
international cement players like Dangote Cements are exporting cheap
cement from Zambia. Thus the Malawian cement companies do not have any
choice but to look at alternatives of reducing production costs,
improving quality and diversifying into speciality products.
Limestone Calcined Clay or LC3
can be a good choice for Lafarge Cement Malawi. LC3 is a
family of composite cement containing clinker, calcined clay and
limestone. The LC3 technology promises a sustainable growth
of economies around the world by reducing CO2 emissions by
more than 30% compared to plain portland cement at lower production
costs. As LC3 cement uses raw materials and technologies that
are already commonly used in cements and can be used in the same way as
normal cements, LC3 provides a practically viable solution to
improve sustainability.
Due to the lower clinker content, LC3
technology has several advantages over Ordinary Portland Cement (OPC)
and fly ash based Portland Pozzolanic Cement (PPC). The main advantages
will be:
-
Improved resource efficiency
-
Lower CO2 emission
-
Enhanced durability of the building
materials and concrete
-
Reduced cost without compromising the
performance of the cement
-
Easy processing and supported by existing
production facilities
LC3 allows a clinker substitution
of around 50-60%, by a synergetic combination of calcined clay and
limestone. For LC3 production, raw clay is usually calcined
by rotary kiln which is continuous in nature and used for large scale
production. Specially for small scale of calcination (<50 tonnes /day),
Vertical Shaft Brick Kiln or VSBK is a better option.
VSBK has several advantages over rotary kiln
as illustrated below:
-
Lower capital investment compared to rotary
kiln of similar capacity
-
Easy operation and lower maintenance cost
compared to rotary kiln
-
Multiple options to reduce fuel cost with
improved fuel efficiency using fuel block/internal fuel for VSBK
-
VSBK can run without electricity whereas
rotary kiln needs 24 hour uninterrupted power supply
-
VSBK creates livelihood and more income
generation opportunity for local people.
Considering the potential advantages of VSBK
as mentioned above, Lafarge Malawi opted for VSBK technology for
calcination of clay in LC3 application. There is a huge
reserve of clay near Lafarge plant at Blantyre. Successful lab and pilot
trials were conducted in Malawi under the guidance of TARA, the social
enterprise wing of the Development Alternatives Group. Lafarge clay was
calcined in VSBK. Standard LC3 batch was produced using the
calcined clay and tested. The new blended cement with 50% reduced
clinker was equivalent to CEMII 42.5R grade. The results were very
promising and reproducible. Consequently, Lafarge Malawi decided to use
VSBK for calcination of clay during commercial production of LC3
in Malawi which is undoubtedly an eco-efficient approach.
■
Endnotes:
-
2018 Malawi Population and Housing Census
Report
-
The 2008 Population Census (NSO 2008, pp.
26)
-
CCODE, Centre for Community Organisation and
Development, a Malawian NGO with focus on low cost housing and slum
up-grading founded in 2003 (www.ccodemw.org)
-
Urs Heierli, Brick by Brick: The Herculean
Task of Cleaning up the Asian Brick Industry
-
Maity, S. & Nagrath, K. (2012): MALAWI,
Feasibility of VSBK Technology for cleaner brick production
-
Clíoma (2013): Brick Production Provisional
Baseline Study
▪ Swiss Agency for Development and Cooperation (SDC), Switzerland
▪ Department for International Development (DFID) UK, through the
Business Innovation Facility (BIF).
Biswajit Swain, Palas Kumar
Halda
bswain@devalt.org,
pkhaldar@devalt.org
Back to Contents
|