Innovations for Climate
Change Mitigation: LC3
Given
the rise in urbanisation, extraction and use of natural
resou rce
materials, further leading to greater generation of waste is bound to
create a vicious cycle of production and consumption. However, several
economies worldwide are attempting to ‘decouple’ use of natural
resources from the growth of the economy. This is referred to as
‘Resource Decoupling’, which means reducing the rate of use of (primary)
resources per unit of economic activity. This understanding of
‘dematerialisation’ is based on the concept of using less materials,
energy, water and land for the same economic output, and it is connected
with an increase in the efficiency with which resources are used (Caleb,
et al., 2017).
Waste Materials and Building Product
Standardisation
Taking this into consideration, the Bureau
of Indian Standards, the National Standards body of the country, has
been considering the scarcity of sand and coarse aggregates from natural
resources, and has evolved a number of alternatives which are aimed at
conservation of natural resources apart from promoting use of various
waste materials without compromising on quality. These measures have
included permitting
the Concrete Code (IS 456) as also in the National Building Code of
India i.e. the use of slag - waste from the steel industry, fly ash
waste - waste from thermal power plants, crushed over-burnt bricks and
tiles - waste from clay brick and the tile industry, in plain cement
concrete as an alternative to sand/natural aggregate, subject to
fulfilling the requirements of the Code.
Further for the 15 varieties of cements, for
which Indian Standards have been developed, more than three-fourth of
the cement produced in the country pertains to Portland Pozzolana Cement
and Portland Slag Cement, popularly known in the market as blended
cements (BIS, 2017). Research continues to take place to increase the
use of supplementary cementitious materials to reduce the clinker factor
in cements.
Innovation for Climate Change Mitigation:
LC3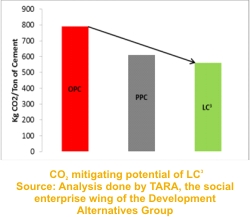
In this sphere, Limestone Calcined Clay
Cement, commonly known as LC3 has made a successful
break-through in both innovation in cleaner technology as well as
resource efficiency and use of secondary raw materials. LC3
provides the perfect cement blend that has a mix design of 50% clinker,
15% non-cement grate (waste) limestone, 30% waste china clay
(overburden) from mines and 5% gypsum. The blend has two major
advantages for sustainable production. Firstly, about 45% of raw
material in the blend is waste and secondly clinker content is reduced
to 50%. Life Cycle Analysis reveals that LC3 production can
reduce carbon dioxide emissions up to 30% and save up to 50% limestone
as compared to conventional cement. The LC3 cement is also
found to have comparable durability and strength as compared to
conventional cement. Further, the most suitable clays for production of
LC3 are overburdens (waste clay) from china clay mines.
Barriers to Upscaling Production of LC3
In the present Indian Standards, replacement
of cement with calcined clay as a pozzolan is limited to 25% (IS 1489)
and limestone as performance improver is limited to 5% (IS 269) (Medepalli,
Shah, & Bishnoi, 2016). Resistance in the standardisation for the use of
LC3 has mainly been in the form of poor technical
understanding of the process and the strong lobby of the Indian
construction sector.
Various structural applications require
various compressive strength and therefore the conventional approach to
‘one-type fits all’ causes a hindrance to innovation and flexibility to
exploit local opportunities for raw materials, both for clinker and for
supplementary materials like fillers.
Thus, while the Indian cement market
continues to wait for the Indian standard on LC3 based
building materials, a necessary change in the standardisation process is
the need for assessment of various applications and the flexibility that
can allow for greater use of supplementary cementious materials (in this
case industrial waste) and thereby reducing the use of natural
resources. This range in standards for materials will ensure a larger
market for building products as well as allow for greater innovation in
increasing the use of waste materials, thus reducing dependence on
natural resources.
Mapping Awareness at the International
Level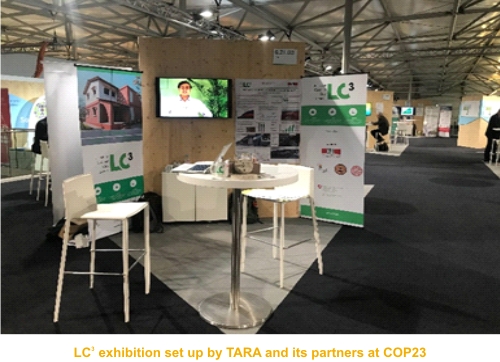
At the international level, LC3
has gained a lot of positive response. Several African countries like
Ghana, Ivory Coast, Togo, Benin, Mauritania, Uganda etc. have shown
interest in identifying the potential of LC3 in their region.
At the recent UN Climate Change Conference (COP23) in Bonn, Germany,
6th- 17th November 2017; TARA, the social enterprise wing of the
Development Alternatives Group along with its project partners set up a
LC3 exhibition to showcase the potential of LC3 in
mitigating climate change.
The cement value chain makes up a large
propotion of all economies, including a range of stakeholders from large
companies to individuals. While the cement industry, especially under
the Cement Sustainability Initiative tries hard to increase efficiency
and environmental sustainability in the sector, commitment of the
government through public procurement policies, stringent policies on
use of natural aggregates and incentives for research and development
are the need of the hour.
■
References:
-
Olivier, J. G.,
Janssens-Maenhout , G., Muntean, M., and Peters, J. A.H.W (2016). Trends
in global CO2 emissions; 2016 Report. The Hague: PBL
Netherlands Environmental Assessment Agency, Ispra: European Commission,
Joint Research Centre.
-
WBCSD. (2015). Low Carbon
Technology Partnerships Initiative-Cement. New York: World Business
Council for Sustainable Development.
-
BIS. (2017). Indian Standards
for alternative materials to natural sand and other natural resources .
Retrieved from Bureau of Indian Standards: Press Release :
http://www.bis.org.in/other/PR_ NSNR.pdf
-
Caleb, P. R., Gokarakonda, S.,
Jain, R., Niazi, Z., Rathi, V., Shrestha, S.,. Topp, K. (2017).
Decoupling energy and resource use from growth in the cnstruction setor:
A baseline study. Dt. Ges. für Techn. Zusammenarbeit.
-
Medepalli, S., Shah, V., &
Bishnoi, S. (2016). Production of Lab Scale Limestone Calcined Clay
Cements using Low Grade Limestone. 7th International Conference on
Sustainable Built Environment.
-
Scrivener, K. L., John, V. M.,
& Gartner, E. M. (2016). Eco-efficient cements: Potential, economically
viable solutions for a low-CO2, cement based materials industry. United
Nations Environment Programme.
-
UNEP IRP. (2011). Decoupling
Natural Resource Use and Environmental Impacts from Economic Growth. A
Report of Working Group.
Pratibha Caleb
pcaleb@devalt.org
Back to Contents |