LC3 – A Viable
Solution for Achieving SDGs
Industrialisation
has brought comfort to our lives, but at the expense of environmental
resources. The quantity of cement produced has increased dramatically
because of the growing world population, economic development and rapid
urbanisation. The volume of cement production by 2050 is projected to be
about 6 billion tonnes. In 2014 alone, 4.2 billion tonnes of cement was
produced globally and accounted for 2.7 Gt of CO2 emissions,
approximately 7% of the total anthropogenic CO2 emissions
worldwide, making cement the second largest carbon dioxide (CO2)
contributor in industry after power plants.
Cement is also a resource intensive material. A
tonne of conventional cement production requires 1.4 tonnes of limestone.
The sheer quantity of cement demand in the future would put measurable and
rapid impact on limestone resources around the world.
The most effective strategy for reducing CO2
emissions and use of natural resources by cement production lies in reducing
its clinker content. This can be achieved by substitution of clinker with
reactive materials, which up to now have typically been industrial by -
products: fly ash from coal fired power stations and blast furnace slag.
However, supplies of these materials are limited compared to the amount of
cement produced worldwide. We also do not want more coal based thermal power
plants in the future. Hence the future availability of industrial wastes is
a question mark.
Koilinitic clays have a considerable potential to replace harmful clinker in
cement. They are widely available naturally and require very simple
processing to be used in cement fabrication. Limestone Calcined Clay Cement
(LC3) exploits this potential and reduces the limestone
requirement in cement by 50% and CO2 emissions by 30%. This is
the innovation of LC3 - to replace clinker with a widely,
naturally available material. The important thing to note is that clay used
by LC3 is of a low quality and is left over as a waste by mine
owners. Thus, LC3 presents an opportunity to use this mine waste
as a resource. Cement companies can easily fabricate LC3 in their
own cement plants without changing their existing processes. A small
investment to purchase and install a kiln is required to calcine the clay.
However, this investment is saved if there is spare kiln available in the
existing production line of the cement company.
Practical experience has shown that the
production of LC3 even under basic artisanal conditions is
possible and produces cement of good quality. This means that the potential
of producing LC3 under optimised industrial condition is highly
attractive and can certainly be mastered by the major cement companies.
Furthermore, a few demonstration buildings - a
house in Jhansi, Central India, some roads and the annex to the Swiss
Embassy in Delhi have demonstrated the feasibility of using LC3
on a larger scale.
LC3 is expected to contribute to the
following SDGs:
SDG 9: Industry, Innovation and Infrastructure
SDG 11: Sustainable Cities and Communities
SDG 12: Ensure Sustainable Consumption and
Production Patterns
SDG 13: Take Urgent Action to Control and Combat
Climate Change and its Impacts
LC3 is an innovative product that has
the ability to reduce emissions and will contribute in reducing virgin
resource use in infrastructure for growing cities. Thus, use of this cement
will help in taking urgent action to combat climate change as given in SDG
13.
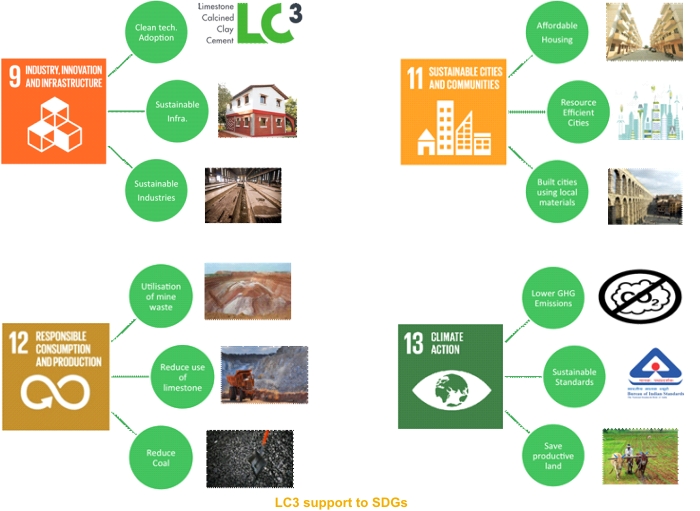
In the Indian context, LC3 can make
important contributions to many of India’s international commitments and
national missions. Some of them are as follows:
• India has committed to reduce the Emissions
Intensity of its GDP by 33 to 35% by 2030 from the 2005 level. Cement
industry in India is a significant contributor to India’s GDP as well as CO2
emissions. Thus, LC3 proposes important contributions in
supporting India towards achieving its INDC. Additionally, the Indian cement
industry over the years has transformed itself tremendously towards
sustainable production of cement and still remains receptive to new
sustainable blends of cement.
• Addressing housing shortage of 2 million units
for non-slum urban poor, the Pradhan Mantri Aawas Yojna (Urban) is being
implemented during the period 2015-2022 and provides central assistance to
Urban Local Bodies (ULBs) and other implementing agencies through States/UTs
for affordable housing, slum rehabilitation etc. LC3 can be a
viable and low carbon initiative to achieve sustainable growth of housing.
• Smart City Mission, an urban renewal and
retrofitting programme aims at renewing 100 cities across India. Thus, there
will be immense amount of cement and concrete needed to cater to this
programme. Fly ash availability is becoming an issue that will affect
production of PPC cement. Hence, LC3 can be an ideal alternative
as resource-mapping studies suggest that china clay availability is spread
across the country.
Economics and standardisation of LC3
are two key levers that can upscale the production and acceptance of LC3
in India. Quality of LC3 as compared to general purpose cement
has already been proven from various lab and field experimentation. However,
cement companies will only produce LC3 at large scale when it is
standardised by Bureau of Indian Standards and has economic viability for
production. The standardisation process in India is slow and complex and
economic viability of cement can only be determined by cement companies, as
financial information is a matter of discretion. However, it is understood
that calcining clay is less costly per tonne than clinker production,
because of the lower energy needed (heating the materials to 750-850°C
instead of 1450°C) provided it can be carried out on a similar scale and
with the same fuel and heat recovery systems as clinker. The cement also
uses less limestone, which indirectly increases the mine life of limestone
and hence positively impacts the revenue of cement companies. Specific
economic advantages are however situation specific and depend on several
factors such as the proximity of clay deposits and substitutes (fly-ash,
slag) and whether new equipment or land is needed for LC3
production, or if under-utilised equipment can be used?
LC3 has made significant technical
progress and has demonstrated enormous potential of savings and the pressing
need to reduce greenhouse gases. It is the right time to put this solution
into the global climate change dialogue where the world is looking for
solutions that can be put to action. Sustainable cement is surely one of the
most important one of them.
■
Vaibhav Rathi
vrathi@devalt.org
Back to Contents
|