Man
is a thinking animal. While thinking and imagining, he tries to carve
small wonders out of his thoughts. From whatever he thinks in his
thoughts, he sees in his dreams, he tries to change things around him. And
these creations become a reflection of his thoughts, his imaginations.
Something of similar nature has happened recently, at the residence of Mr.
Rajiv Sethi, one of the renowned designers of India.
The idea was born with the search for a perfect
place where he could relish his mornings with all his amazing ideas.
He decided to transform his terrace into such a place. As a part of it, he
imagined a flying scoop projecting out of the terrace, which apart
from its functional use, would take his ideas into the universe of
creativity and imagination.
In his quest, he was accompanied by a team of dream
weavers from Development Alternatives who through their genuine effort
transformed the idea into a reality.
In the nitty-gritty of it all...
It would be interesting, to detail out the technical
side of this process for professionals working in the field.
The working team first looked at the design of the
scoop and existing site conditions where the structure was to be built.
Seeing the particular shape, size and ground conditions, it was decided to
precast the structure away from the site. Ground layout and mould
construction commenced at the building centre, TARA Nirman Kendra, around
15 km away from the site. The precision in the non-uniform design,
particular details and shape required much attention. The machine design
team of Development Alternatives played an important role in keeping the
mould construction as close as possible to the structure on paper. As a
part of a multi-design process, another critical step was the structural
design of the scoop, which was worked out by a senior engineer in the
team.
This world is full of surprises...isn’t it
On completion, the mould appeared (turned out) larger
than assumed. But then, with a sigh we convinced ourselves that it was due
to the inverted construction of the mould.
Now was the time for casting, which was preceded by
activities like wire mesh cutting, reinforcement binding and side
formwork. On anticipating the process for installment, the team cast the
whole structure in 6 smaller panels. While the panels were cured, the
construction crew started with the necessary on-site activities, which
were required to place and anchor the cast panels.
Its time for delivery.....
After curing, came demoulding and transportation. All
the panels were demoulded carefully and were loaded with gingerly hands,
onto two trucks. Equally tedious were getting these panels off the trucks
manually, which was brought about with help of jute ropes and wooden
ballis.
Phew! We could sense the feeling of ACHIEVEMENT
throbbing in many hearts.
After this exercise the team realised that it would
require a mechanical device, for lifting these panels to the second storey
and installing them in-place.
The Grand Finale…..
The construction crew was all set and the finale
started with the arrival of a boom crane.
The mechanical giant extensively helped in lifting the
panels and placing them in exact positions, allowing the anchor bolts
passing through the holes. To provide the manual support from the
cantilevered portion, temporary platforms were built using toe boards and
scaffolds. Then, a little alignment, joining of the reinforcement, in-situ
casting and some finishing touches transformed the uneven, rugged,
individual concrete panels into a large, solid and graceful piece of
craftsmenship.
So this is the long and short of a happening.
A happening which would be in our minds for long,
because at its heart there is lots of enthusiasm and spirit of teamwork. q
|
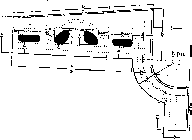
|