Natural Fibre Composites -
a new application in bamboo technology
Bamboo
has a long and well established tradition as a building material
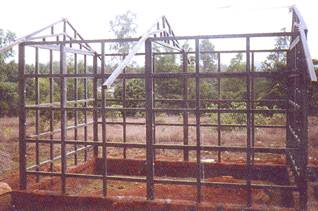 |
Structural frames
for shelters made
out of Bamboo based NFC elements |
throughout the world’s
tropical and sub tropical world. It is widely used for many forms of
construction , specially for housing in rural areas. It is a fast
growing, renewable and versatile resource, characterized by high
strength and low weight, and is easily worked upon using simple
tools. Bamboo constructions are easy to build and with correct
details are resilient to wind and earthquake forces with correct
details. Yet, the use of bamboo has been largely restricted to
temporary structures and lower grade buildings due to limited
natural durability, difficulties in jointing, flammability and lack
of structural design data.
Moulded
in different shapes….
Perhaps,
one of the biggest advantages of bamboo is the versatility in the
forms and the composites it can be used in. It can be used in
conjunction with other materials while offering excellent structural
properties. One such application is the use of bamboo in Natural
Fibre Composites (NFC). Bamboo forms the core material which is
encased within resin to give monolithic structural elements. The
intermeshing of fibre to resin combination gives a dense matrix of
high strength and a relatively light composite material. The bamboo
core can be customized to different applications- small bamboo
culms, split bamboo, flattened bamboo, bamboo mats,etc. After
cutting the bamoo in the required shape and size, it is placed in
the mould, similar to laying a reinforcement cage and the resin is
poured into the forms to encase it. The resin is mixed with
accelerators and hardeners according to specifications to make it
ready for use.The demoulding time varies from 40 minutes to 2 hours.
Many
applications
By using
moulds of different geometries, a series of shapes and sizes for
different applications can be achieved. NFC materials can be moulded
into sheets, boards, gratings, pellets, frames, trench covers, stair
treads etc. Many structural sections can also be fabricated like
beams, columns, trusses, purlins and rafters. This makes it possible
to use them in prefab housing, cubicles, kiosks, sheds and even
geodesic domes and pyramids. They can also be used as a substitute
for wood, metal or masonry for partitions, false ceilings, fences,
railings and even as flooring roofing and walling tiles.
The use of
resin
The use
of resin imparts resistance to chemicals like acids and solvents,
thermal and electrical resistance and makes the composite water
proof, termite proof, rot proof . This makes the product ideal for
use in wet environments and other extreme conditions like
industries.
 |
A truss of
7 ntre span weighting
around 55 kg. |
The
material can be potentially very cost effective since a large
proportion of the end product comprises of bamboo or other natural
fibres or agro based biomass of different varieties. The use of
resin is the influencing factor in determining the cost of the
material. The percentage of resin in the finished product depends on
its shape and size. In smaller and thinner products like gratings
and tiles, the proportion of resin can be 50- 60 %, whereas in
structural elements like trusses and beams, it can be 25- 30 %.
Since, resin is the only industrial product used in the technology,
the rationalized use of resin in the elements will not only further
bring down the cost of the technology but also make it more
environment friendly.
q
Reported by Pankaj Khanna
For more information on the technology
contact Mr. Khare
Shree Bhargav Fibres, Pune
E-mail : sparkonix@vsnl.net
FC
Roof Channels manufacturing and marketing
- Experiences in Himachal Pradesh
Subodh Abbhi farmfood@sancharnet.in
We
run a precast concrete products unit located in the village
Batamandi of Sirmur District in Himachal Pradesh on the banks
of the river, 7 km from Paonta Sahib.
Four years ago we started manufacturing ferrocement roof
channels with technology and machines sourced from Development
Alternatives New Delhi. We used these channels in a roof of
our office and have never looked back. Several asbestos cement
roofs in our unit were replaced with ferrocement channel
roofs. All roofs in our campus are now of ferrocement and
cover approximately 5000 sq. ft. area. Several industrial
units in the neighbourhood too adopted these ferro roofs in
their buildings.
These buildings invite interest from far and near. An army
veteran used these for a school he was running in Uttranchal
near Dehradun. An industrialist of Yamunanagar adopted the
roof channels for a ramp drive leading to the first floor of
his house where he installed another ferrocement channel roof
for a lawn and the area below for living quarters and storage.
A farmer of a village near Nahan constructed his two storied
house with roof channels, and walls of interlocking earth
bricks. He is a very happy customer who firmly believes that
the ferrocement technology made possible a shelter at almost
50 percent of the cost.
Problems
Leakage of water from the joints has been a major factor
against the use. Our experience shows that this can be
corrected by forming and curing the joint with a layer of
Ferro cement and then putting concrete for making the slope.
Handling of the roof channels has been a major problem but it
need not be so when a person is convinced that the channels
are the right option for his roof. It has been convenient to
lift the channels from the truck directly on to the roof with
the assistance of a crane or chain pulley block fixed on to a
vertical steel mast. The farmer from Nahan carried the roof
channels by head load for a distance of 2 km for his double
storied house as there was no road to his village.
The
technology is acceptable to people here but the shape deters
most of them. The poor do not adopt it as they probably do not
want something which is not approved by the Block office and
therefore not subsidised through a government scheme. The
block people do not recommend the construction method as they
loose on the commissions for the building material used in the
subsidized houses.
However, our experience has established this technology as a
viable option for economical shelters, without any shortfall,
in strength and aesthetics when compared to the conventional
RCC slab.
q
|
Back to Contents
|