Affordable Housing in the Context
of Sustainable Habitat
T he
EWS and LIG constitute more than 99 per cent share of total housing
shortage of 24.71 million in India (figures from Planning Commission
Report 2007). This number is further expected to increase to 26.5
million by 2012. This is due to the large number of people at the bottom
of the economic pyramid. The business viability of this sector has
already been established with market researches. The obvious logic here
is that such a large number of people, with limited amounts of cash put
together, have a considerable buying potential.
Building Industry
and Climate Change
The climate is changing. The earth is warming up, and there is now
overwhelming scientific consensus that this is human induced. With
global warming on the increase and species and their habitats on the
decrease, chances for ecosystems to adapt naturally are diminishing.
Climate change may be one of the greatest threats facing the planet.
The building and construction sector is a key contributor to the
phenomena of climate change. The built environment accounts for a large
share of energy use (with associated greenhouse gas emissions), waste
generation or use of natural resources. Areas of key concern also
include production of construction materials, use and recycling,
consumption of hazardous materials, integration of buildings with other
infrastructure and social systems, water use and discharge, etc. The
construction industry is estimated to be responsible for around 40 per
cent of the total carbon emissions globally. Buildings are responsible
for large shares of resource use and waste generation: approximately 40
per cent of materials use, 30 per cent of solid waste generation, and 20
per cent of water use. The materials and technologies used in buildings
also have a significant impact on their users’ health and well being.
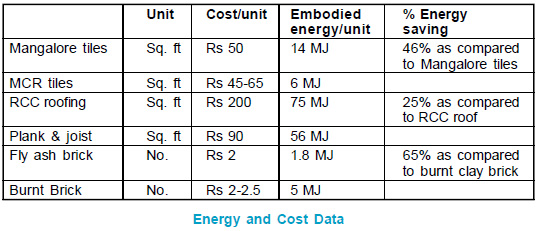
Compared with many other industry sectors, the opportunities to reduce
emissions are easier to achieve and also more substantial. Energy use in
buildings can typically be reduced by 50 per cent or more using proven
and commercialised technologies and approaches. This sector has the
potential to lead the fight against climate change.
The huge volume of housing to be constructed, especially that in the
affordable sector can have a huge role in this direction towards
lowering carbon emissions. It has been seen that typically a house made
using appropriate technologies has the potential to reduce at least 25
per cent of energy input itself, which can prove to be a tipping point,
considering the scale of construction. With the Prime minister’s
National Action Plan on Climate Change having a sub-mission on
sustainable habitat, the issue takes a completely new dimension in the
Indian context.
The Model Eco
Village Housing
The village in question is Guru Nanak Dev Nagar, village Gaggar,
district Muktsar, Punjab. This project was conceived by the Punjab
Government to provide shelter to the BPL families of the village. The
project was started by Ambuja Cements Foundation in collaboration with
the GoP in 2008 and was completed in August 2009. In all, 129 houses
have been constructed with the cost of a single house being Rs 1.7 lakh,
at around Rs 470/sq ft. Each house with a covered living and cooking
area of 370 sq ft and a bath and toilet of 15 sq ft is built on a plot
of 1200 sq ft. A single house has two rooms, a kitchen and a bathing
area and toilet. Each plot has space for a cowshed and a cycle/scooter
shed and the possibility of vertical expansion with another floor that
may be added as the family size increases.
Technology
Description
The house has a conventional brick foundation. The walls are made using
fly ash bricks in rat trap/rowlock bond. The roof of the main built
volume is in precast plank and joists. This is then topped with a
weather proof course of brick tiles on mud phuska over bitumen PCC
screed. The roofing over verandah and the kitchen is done using Micro
Concrete Roofing (MCR) tiles with MS rafters and purlins. Local masons
were trained in the usage of these technologies by TARA Nirman Kendra
(TNK), a building centre of the Development Alternatives Group
specialising in green building materials and habitat design. This
training was conducted on a demonstration house at the site.
Roofing:
Pre-fabrication for Cost Savings
Incorporating pre-fabricated plank and joist roofing significantly
lowered the construction costs. Plank and joist roof with the three
layered weatherproof course have worked out to be 20 per cent cheaper
than conventional RCC roof. It took two days for roof construction,
including finishing the assembly of prefabricated components with screed
concrete, saving at least 10 man-days per house in addition to savings
on scaffolding and curing period of 21 days for each house, which
amounted to further construction efficiencies.
An existing local enterprise of fly-ash bricks, situated around 40 km
from the project site, was trained in the production and quality control
of planks and joists while MCR tiles were sourced from another small
entrepreneur in Chandigarh. The technology transfer was undertaken by
TNK. The casting and curing was done at the production facility with
strict quality checks.
Walling:
Utilisation of Industrial Waste
Waste fly ash generated by the GND thermal power plant at Bathinda was
used in making the fly ash bricks for wall construction. The bricks are
made using the FaL-G technology which uses a mix of fly-ash (50 per
cent), coarse sand (40per cent), lime and gypsum (together 10per cent)
and cement (less than 1per cent). The lime and gypsum are also waste
materials sourced from an oxygen plant and fertiliser plant
respectively.
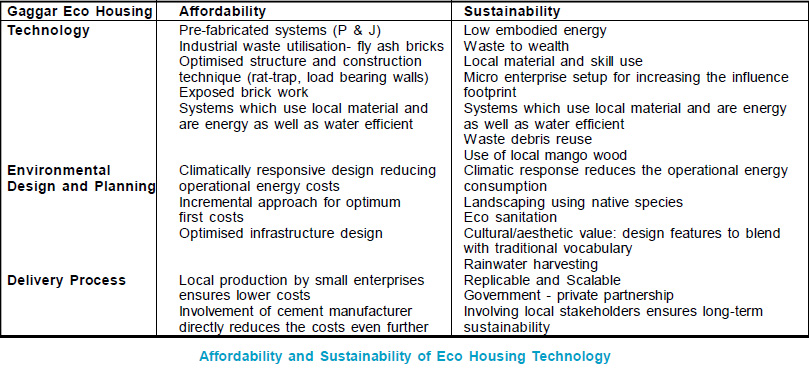
The house
has load bearing 9" thick fly ash brick walls. Red bricks were used in
an interspersed manner (up to 10 per cent of the total bricks used in a
house) to provide relief from the otherwise grey colour of fly-ash
bricks and improve the aesthetic aspect of the house. Usage of Rat-trap
bond for wall masonry which incorporates a cavity within the 9" wall
thickness reduced the brick requirement by 20 per cent per cubic meter
of wall. This reduces the load of the superstructure on the foundation,
resulting in savings due to optimised foundation design as well.
Similarly, mortar requirement is reduced by 20 per cent (as compared to
conventional English Bond) for a 1:4 cement-sand mortar. Apart from
this, construction by trained masons ensures superior quality of
brickwork, obviating the need for cement plaster. The exposed brickwork
has led to 15 per cent of overall cost reduction. Locally made pre-cast
cement jaalis have been used to look out into the verandah. Doors and
windows were made using local mango wood.
Rainwater from each house is directed through drains to harvesting pits
located in the central parks of the settlement. Bathinda region receives
approximately 410 mm of rain annually. The water harvesting system
designed in the settlement is expected to catch 80 per cent of
precipitation on the site (approximately 10,000 cubic meters) both
through street drains as well as roof rainwater drains and direct these
for recharging the aquifers.
The toilets constructed by Sulabh International have the twin-pit
system, which uses each pit alternatively in a cycle of around three
years to percolate wastewater and, at the same time, decompose the
faecal matter into organic manure. Cost of a complete toilet, including
squatting pan, plumbing, finishes, etc., is approximately Rs 7,500.00.
Technology
vis-à-vis Sustainability
One of the key measures for ecological sustainability of building
technologies is embodied energy. Embodied energy represents the
non-renewable energy consumed in the extraction of raw materials, their
processing, conversion to building materials (manufacturing),
transportation to site and construction using the building material. Low
embodied energy of the material signifies that the net carbon emissions
during the production, transportation and construction of the building
element are also low. So the lower the embodied energy, the higher it
ranks in its ecological sustainability.
Pre-fabricated components generally have lower embodied energy in
comparison to the cast in situ elements due to both enhanced production
efficiency and reduced requirement of high energy raw materials.
The third aspect here is the usage of industrial waste like fly ash for
construction. The ecological advantages are twofold, it utilises an
industrial waste and prevents the usage of potentially fertile
agricultural land. Bricks are hydraulically compressed and not baked,
which eliminates both usage of burning fuel and the emissions associated
with it. Also, as the quality of the bricks is superior with controlled
dimensions, well formed edges and surfaces, it removes the need for
plastering, further reducing the embodied energy of the walling system.
Unbaked MCR tiles as a replacement for market standard, high energy
asbestos sheeting and Mangalore tiles can save up to 46 per cent energy.
Design and
Planning
Around 20 houses form a cluster around a central green open space. The
central movement spine links the two main access routes to the site. All
the roads are soft paved. Rainwater falling on the pavements is drained
into the green areas for percolation. Native trees and shrub species
were planted to create a wholesome environment.
Incremental Model
for the House Design
Each house has been designed to allow for future expansion. A flat roof
aids such an incremental approach and also optimises the first costs to
the investor, where only the minimum space requirements of the customer
are catered to and any future modification and customisation lies at the
discretion of the user.
Climatically
Responsive Design
The houses are designed to respond to the hot and dry climate of the
region. Openings are so designed so as to ensure cross ventilation and
adequate shading by chhajjas. Openings on the south side of the houses
are avoided. A weatherproof layer has been added on the top of each
house.
Optimal Sanitation
Systems
The sanitation system provided by Sulabh International under the total
sanitation mission uses water efficient pour flush toilets with twin-pit
leach pits. Adequate care is taken to ensure that leach-pits are at a
suitable distance from the water source – that is piped to the
settlement. Vernacular design features like aara (niche) in main
entrance wall and traditional brick parapet patterns were incorporated
in the house design to integrate it with the cultural psyche. The
intention was also to bring about a perception shift in the local
community, who associate low-cost housing with bland looking boxes.
Delivery Process
The Ghaggar eco-housing was a government-led project where land and
infrastructure were provided by government or quasi government agencies.
The land was provided by the Zila Panchayat, the plantation in the green
areas was undertaken by the forest department, water supply by the
public health department and the roads and park boundaries were set up
by the Punjab Mandi board. The government collaborated with the private
sector in this case ACF of Ambuja Cement Limited as part of its CSR
function facilitated its Foundation for financing and management of the
project. ACF hired TARA Nirman Kendra (TNK) of the Development
Alternatives Group as a technical consultant to the project. The
eco-housing was designed with affordability and sustainability as key
concerns. TNK trained the local masons and undertook the technology
transfer of appropriate technologies to a local entrepreneur to ensure
quality fly-ash bricks and prefabricated plank and joist roofing.
Individual plot holders, all in the BPL and landless category, were
identified by the local committee formed by the Panchayat. This
committee was guided by ACF during the implementation period.
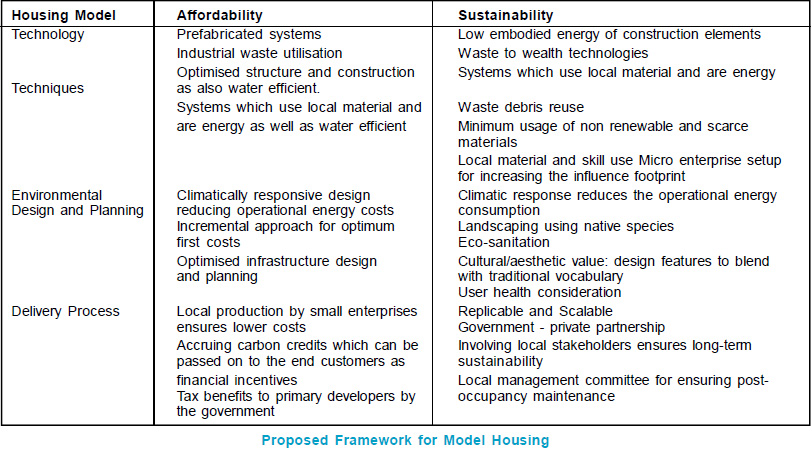
Lessons
The lessons are summarised in the framework where the interconnected
criteria of technology, environmental design and planning and delivery
processes are evaluated against the affordability and sustainability
parameters.
Criteria with
Affordability and Sustainability as Parameters
An approach of appropriate systems has affordability as the objective
and economic, social and environmental sustainability are the foundation
of habitat provision. It becomes even more important to have
sustainability as an underlying layer in all affordable housing
initiatives. This is because sustainable measures can not only reduce
the actual construction cost as well as post occupancy operational
costs, but also significantly help in reducing the now, almost certain,
(impending) economic offsets of climate change adaptation.
Delivery Mechanism
of Affordable and Sustainable Habitat
Affordable housing in the larger sustainable habitat framework implies a
three-pronged approach of social, economic and technological
interventions in the housing delivery mechanism. This is a complex
cyclical process with the policy level interventions forming the overall
guiding force. The three interconnected loops converge towards the
central objective of affordable and sustainable habitat, of which
housing is the most important module. Capacity building of local
enterprises is imperative to the process since it makes the model
replicable on a larger scale, resulting in even lower costs.
Conclusion
Affordability of housing should be reinterpreted in terms of its social,
economic and ecological costs and benefits. The built as well as natural
environments are integral to the economic capital of the habitat.
Environmental design and planning should take into account the climatic
response, waste and water management and eco-sanitation, contributing
towards pre- and post-occupancy affordability and sustainability. The
overall housing delivery mechanism should take into account the role of
different stakeholders and have social, economic and technological
measures for affordable housing in the larger context of sustainability.
q
Pankaj
Khanna
pkhanna@devalt.org
Akshay Goyal
agoyal@devalt.org
Back to Contents
|